Australian Property Journal recently reported on some of the key findings from Prological’s latest white paper: 𝘙𝘦𝘵𝘩𝘪𝘯𝘬𝘪𝘯𝘨 𝘸𝘢𝘳𝘦𝘩𝘰𝘶𝘴𝘦 𝘥𝘦𝘴𝘪𝘨𝘯: 𝘐𝘯𝘵𝘦𝘨𝘳𝘢𝘵𝘪𝘯𝘨 𝘪𝘯𝘯𝘰𝘷𝘢𝘵𝘪𝘰𝘯, 𝘧𝘳𝘰𝘮 𝘤𝘰𝘯𝘤𝘦𝘱𝘵 𝘵𝘰 𝘥𝘦𝘭𝘪𝘷𝘦𝘳𝘺.

Rethinking warehouse design
Prological is driving a new way of thinking about property.
Download our whitepaper to find out how you can achieve a more cost efficient and people-centric work environment.
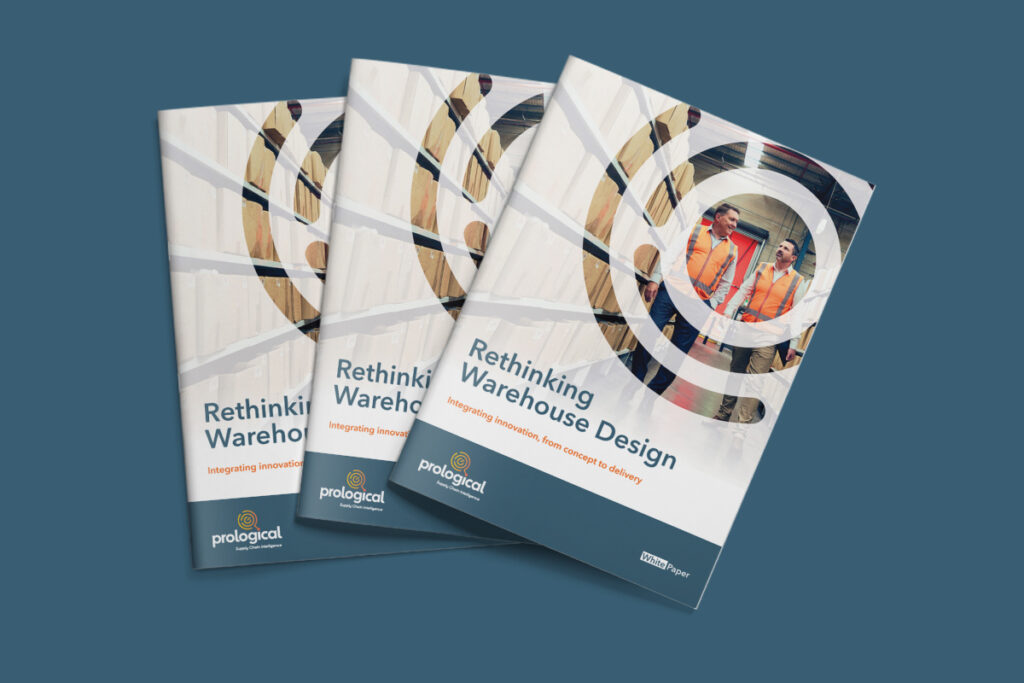